In the realm of manufacturing and engineering, the precision and performance of gears play a pivotal role in ensuring the efficiency and reliability of countless mechanical systems. As technology continues to evolve, so do the methods and tools for measuring, inspecting, and ensuring the quality of gears. In this article, we will delve into the remarkable advances in gear measurement, inspection equipment, and quality control methods that are revolutionizing the industry.
1. Introduction to Gear Measurement Technology
The accurate measurement of gear components is fundamental to maintaining high-quality standards in the manufacturing process. With the advent of advanced coordinate measuring machines (CMMs) and gear measurement systems, manufacturers are now able to conduct comprehensive and precise measurements of gear parameters such as tooth profile, pitch, concentricity, and surface finish. This technology enables the evaluation of gear geometry with unparalleled accuracy, leading to improved performance and durability of gear systems.
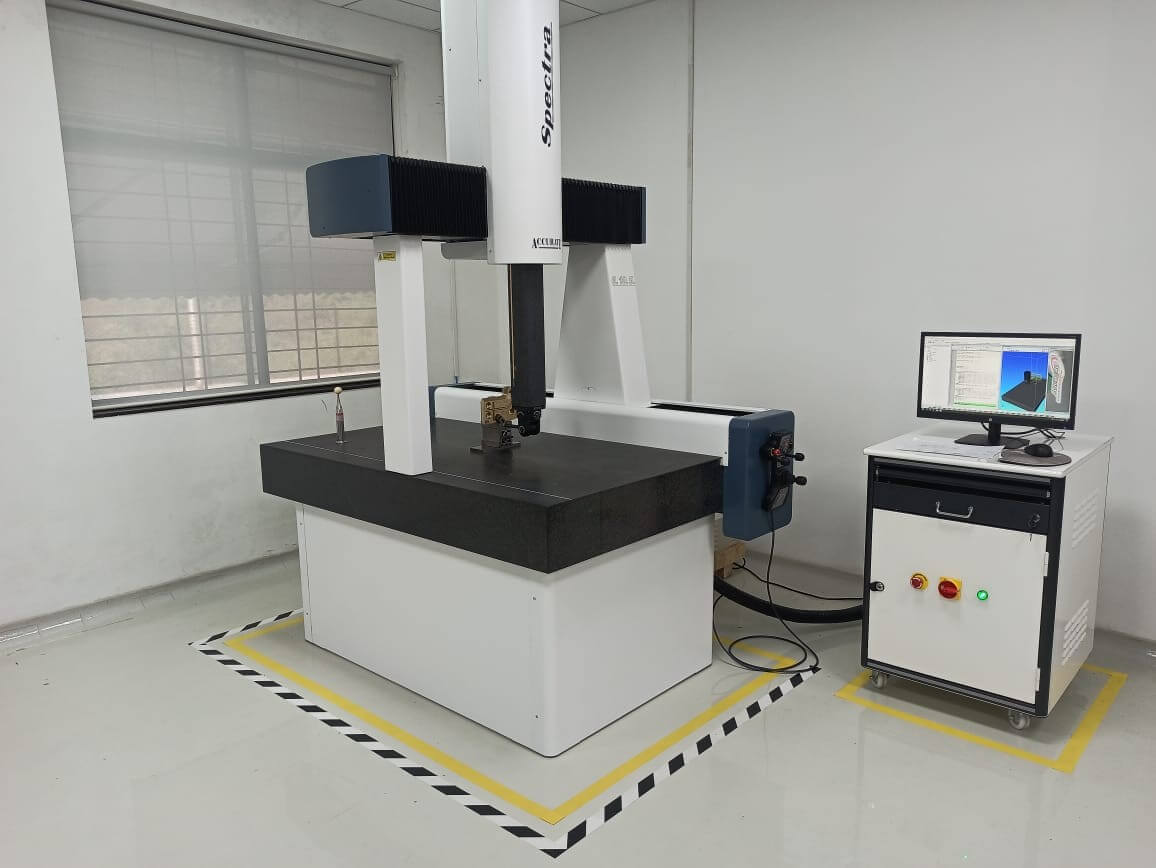
2. Optical Metrology for Gear Inspection
Optical metrology has emerged as a cutting-edge method for inspecting gears with unparalleled speed and accuracy. Utilizing techniques such as laser interferometry and digital holography, optical metrology systems can capture detailed 3D surface profiles of gear components, facilitating in-depth analysis of surface features, micro geometry, and tooth wear patterns. These non-contact measurement methods have significantly enhanced the inspection capabilities while minimizing the risk of damaging delicate gear surfaces.
3. Gear Quality Control via Advanced Non-Destructive Testing (NDT)
Non-destructive testing (NDT) techniques have undergone significant advancements, providing engineers with powerful tools for assessing the integrity and quality of gears without causing any damage to the components. Innovations in NDT technologies, including phased array ultrasonic testing (PAUT) and eddy current testing, have elevated the ability to detect internal imperfections, material defects, and discontinuities within gears, ensuring that only flawless components are integrated into critical mechanical assemblies.
4. Utilization of Artificial Intelligence (AI) in Gear Inspection
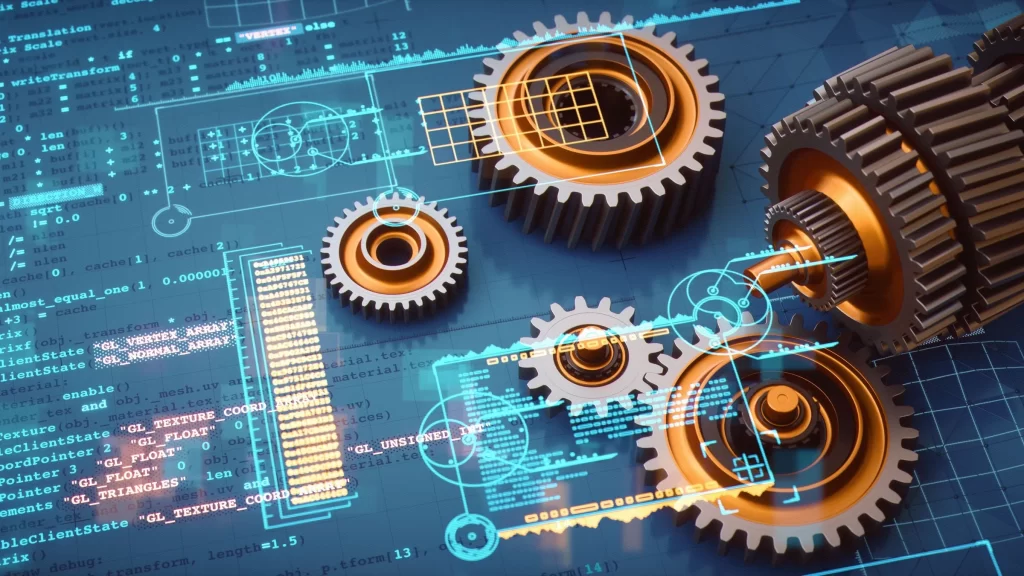
The integration of artificial intelligence and machine learning algorithms has opened up new frontiers in gear inspection and quality control. AI-powered inspection systems can process vast amounts of data collected from gear measurements and NDT processes, identifying patterns, anomalies, and potential failure modes with unparalleled efficiency. This capability allows for predictive maintenance strategies and real-time decision-making, ultimately optimizing the performance and longevity of gear-driven machinery.
5. Advancements in In-Process Inspection Techniques
Traditional gear inspection methods often involved post-production checks, which could lead to costly rework or scrap in the event of non-conformities. However, modern in-process inspection techniques, such as in-line metrology and integrated scanning systems, have revolutionized the approach to quality control by enabling real-time monitoring and correction of manufacturing processes. This advancement not only reduces production lead times but also ensures that gears conform to stringent quality specifications throughout the entire manufacturing cycle.
Conclusion
The continuous evolution of gear measurement, inspection equipment, and quality control methods has instigated a paradigm shift in the manufacturing industry. The amalgamation of precision metrology, non-destructive testing, AI-driven analytics, and in-process inspection has not only enhanced the quality and reliability of gears but has also paved the way for unprecedented levels of efficiency and innovation in mechanical engineering. As we look to the future, these advances will undoubtedly play a pivotal role in driving excellence and sustainability across diverse sectors reliant on gear technology.