Outsourcing manufacturing to Vietnam has become an increasingly popular choice for businesses looking to take advantage of cost-effective production capabilities while tapping into the country’s skilled labor force. However, despite the numerous advantages, there are certain risks associated with outsourcing manufacturing processes such as casting, injection molding, and precise engineering to Vietnam. Understanding these risks is crucial for businesses considering this option, as it allows them to make informed decisions that align with their long-term strategic goals.
Casting
One of the key risks associated with outsourcing casting processes to Vietnam is the potential for inconsistency in quality. While the country boasts a growing number of foundries and casting facilities, there may be variations in the quality of materials and processes used. Lack of standardized quality control measures and varying levels of technical expertise among different facilities can result in inconsistencies in the final product. Moreover, language and cultural barriers can sometimes lead to miscommunications, which may further impact the quality of the casted components.
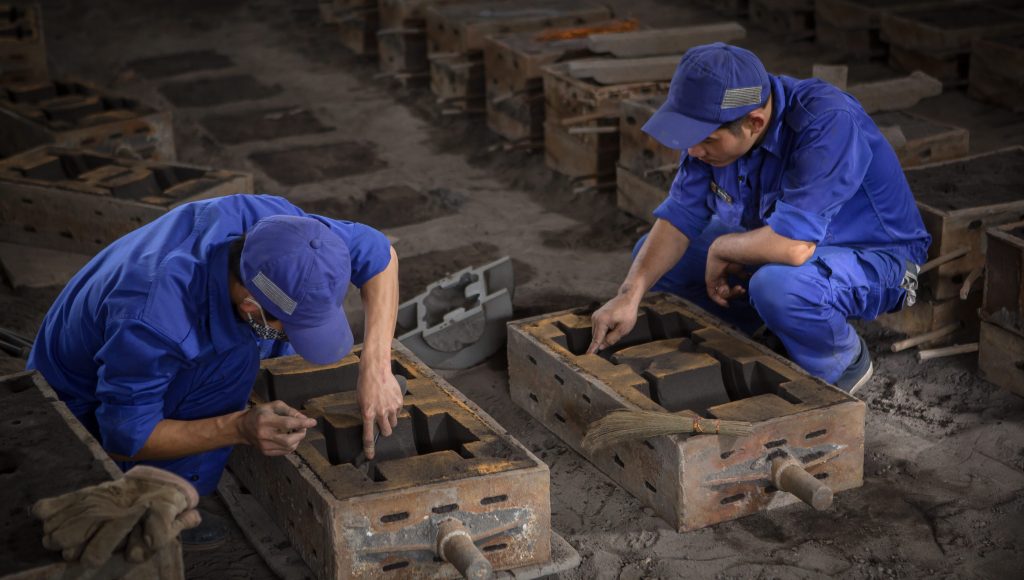
Injection Molding
When it comes to injection molding, businesses considering outsourcing to Vietnam should be aware of certain risks. The primary concern revolves around intellectual property protection. Vietnam’s legal framework and enforcement mechanisms for intellectual property rights may not be as robust as those in other countries, leading to potential risks of design theft or unauthorized replication of molds and parts. Additionally, fluctuating regulations and environmental standards may pose challenges in ensuring compliance with international quality and safety norms.
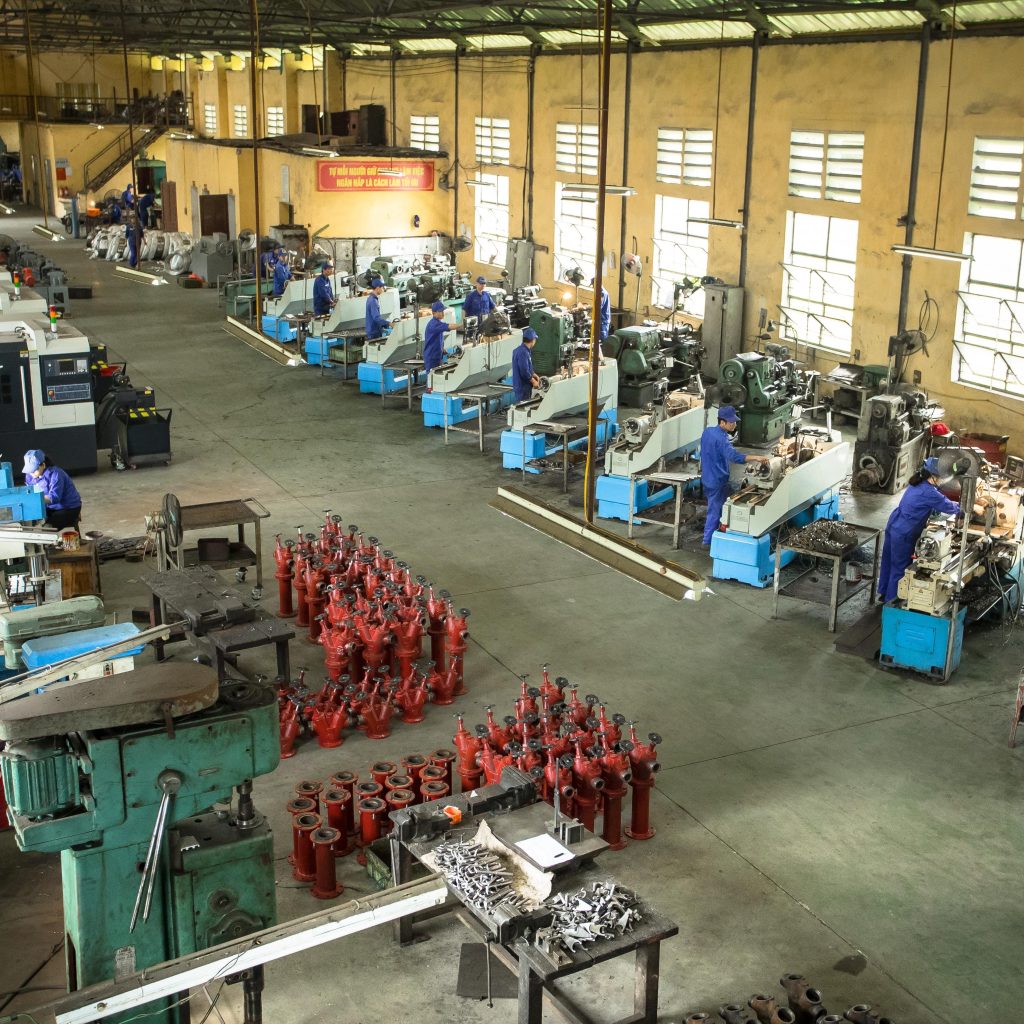
Precise Engineering
Outsourcing precise engineering processes to Vietnam presents its own set of risks. While Vietnam has made significant strides in developing its engineering capabilities, there may still be concerns related to the precision and consistency of the finished products. Factors such as access to advanced technology, skilled workforce, and adherence to stringent quality control standards can vary across different manufacturing facilities. This can result in challenges related to maintaining the desired level of accuracy and precision in the engineered components.
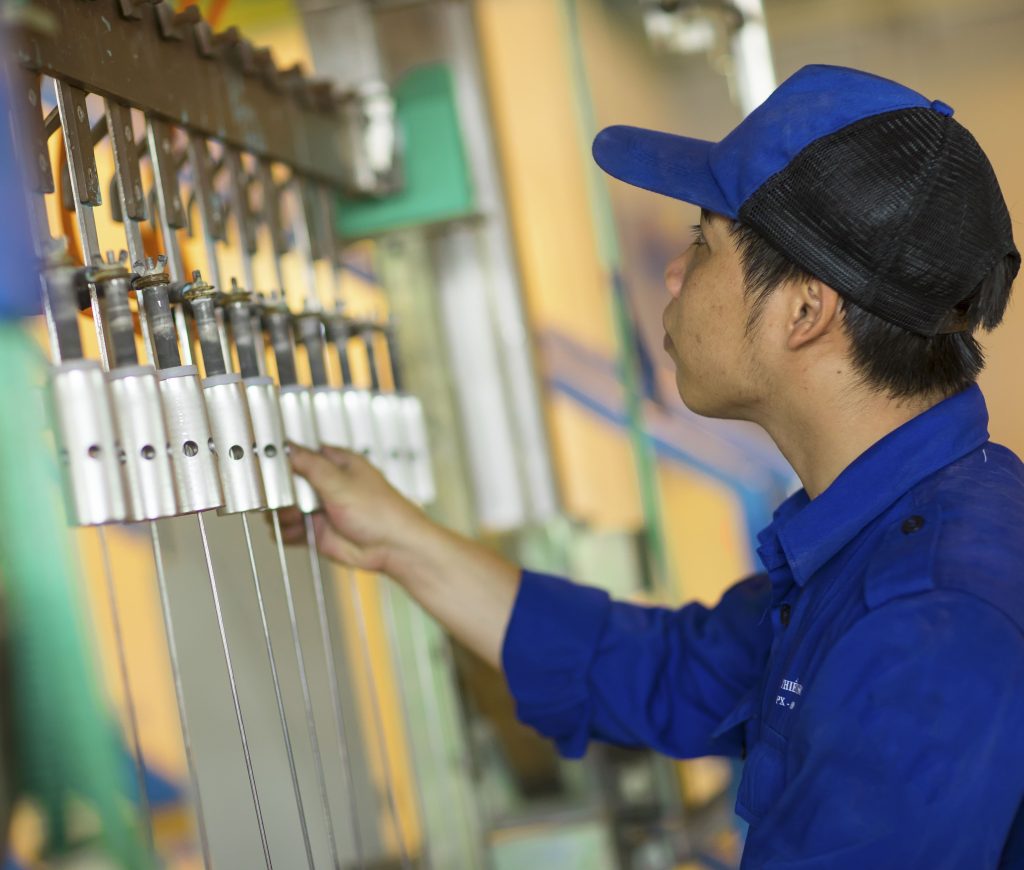
Mitigating the Risks
Despite these risks, there are proactive steps that businesses can take to mitigate the potential pitfalls of outsourcing manufacturing to Vietnam. Prioritizing due diligence in selecting the right manufacturing partners is essential. This involves thorough assessments of the facilities’ capabilities, quality control procedures, and adherence to international standards. Engaging in open and transparent communication, setting clear expectations, and establishing robust contracts with legal protections for intellectual property rights are also crucial steps to safeguard business interests.
Furthermore, establishing strong relationships with local representatives or consultants who are well-versed in Vietnam’s business landscape can provide valuable insights and support in navigating potential challenges. Conducting regular audits and quality checks, and fostering a culture of collaboration and knowledge transfer can also contribute to minimizing the identified risks.
In conclusion, while there are inherent risks associated with outsourcing manufacturing processes such as casting, injection molding, and precise engineering to Vietnam, businesses can effectively manage and mitigate these by exercising due diligence, proactive communication, and strategic partnership development. By understanding the nuances of the Vietnamese manufacturing environment and taking deliberate measures to address potential challenges, businesses can capitalize on the country’s strengths while minimizing the associated risks.