In the realm of power transmission, gears play a pivotal role in ensuring smooth and efficient mechanical operations across various industries. Traditionally, gears have been manufactured using metals such as steel, brass, and bronze due to their excellent mechanical properties. However, the landscape of gear manufacturing is continually evolving, with the integration of new materials presenting unprecedented opportunities to enhance gear performance, durability, and efficiency.
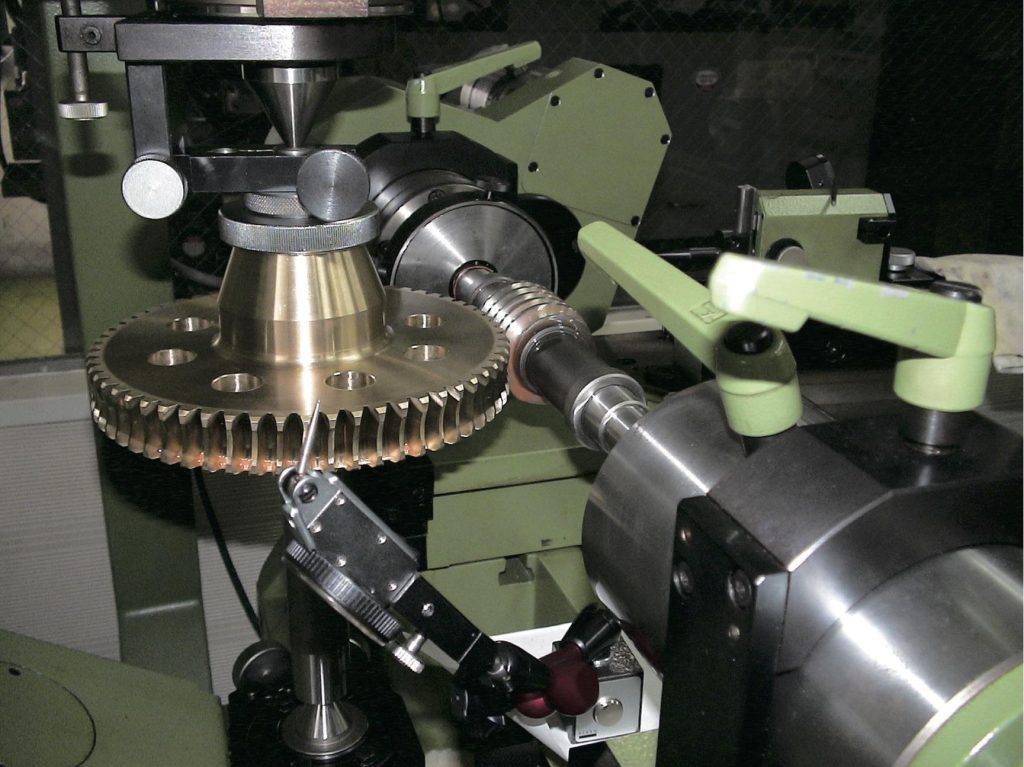
The Emergence of New Materials in Gear Manufacturing
In recent years, advancements in material science have led to the development and adoption of novel materials in gear manufacturing. These new materials encompass a broad spectrum ranging from advanced polymers and composites to cutting-edge alloys and ceramics. Each material brings distinct properties and benefits, revolutionizing the way gears are designed, produced, and utilized in various applications.
Impact of New Materials on Gear Performance
Enhanced Strength and Durability
New materials, such as advanced polymers and composites, demonstrate exceptional strength-to-weight ratios and superior fatigue resistance. This translates to gears that are not only lighter but also significantly more durable, enabling them to withstand higher loads and prolonged operating cycles.
Reduced Weight and Friction
The introduction of lightweight materials in gear manufacturing contributes to the reduction of overall system weight, leading to improved energy efficiency. Additionally, certain materials possess inherent lubricity, resulting in reduced friction and wear within gear systems, thereby enhancing their longevity and performance.
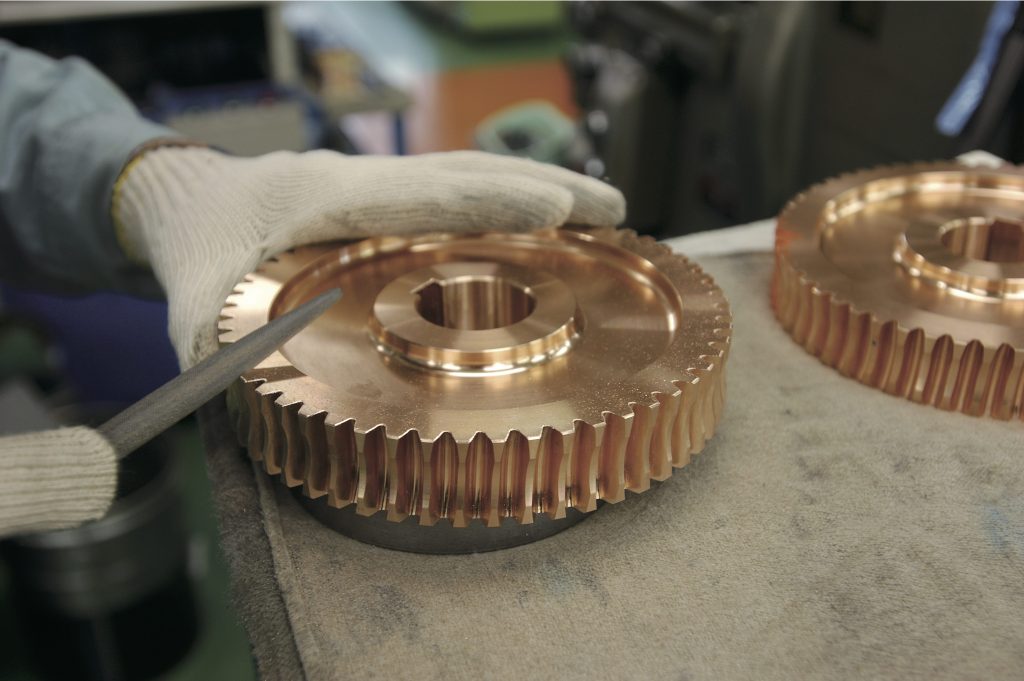
Customized Application-Specific Properties
Unlike traditional materials, new materials can be tailored to exhibit specific mechanical, thermal, or chemical properties to meet the demands of diverse gear applications. This customization allows for the development of specialized gears capable of operating in extreme conditions or performing intricate tasks with precision.
Noise and Vibration Dampening
Certain new materials offer inherent damping properties, effectively mitigating noise and vibration within gear assemblies. This is particularly crucial in applications where noise reduction and smooth operation are critical factors.
Corrosion Resistance
Several new materials possess excellent resistance to corrosion and chemical degradation, prolonging the lifespan of gears used in harsh environments or exposed to aggressive substances.
Case Studies and Industry Applications
The impact of new materials on gear performance is exemplified across various industry sectors:
- Aerospace and Defense: Lightweight, high-strength composites are increasingly utilized in the production of gears for aerospace applications, enabling significant weight savings without compromising performance and reliability.
- Automotive and Motorsports: Advanced alloys and carbon fiber-reinforced polymers are transforming gear manufacturing in the automotive industry, delivering enhanced efficiency and performance in transmission systems.
- Renewable Energy: Gears manufactured from specialized polymers and ceramics are contributing to the advancement of wind and tidal energy technologies, offering greater durability and resistance to environmental factors.
Challenges and Considerations
While the integration of new materials presents numerous advantages, their adoption in gear manufacturing is not without challenges:
- Cost and Scalability: Initial material costs and challenges associated with large-scale manufacturing processes may impact the widespread adoption of certain advanced materials.
- Compatibility and Standards: Ensuring compatibility with existing gear designs and adherence to industry standards is crucial when introducing new materials to established applications.
Future Perspectives and Conclusion
The continual evolution of material science promises further breakthroughs in gear manufacturing. Future developments may see the emergence of self-lubricating materials, advanced nanocomposites, and materials designed for additive manufacturing, further revolutionizing the performance and capabilities of gears across industries.
In conclusion, the integration of new materials in gear manufacturing is propelling the industry toward unprecedented levels of performance, efficiency, and reliability. With ongoing research and collaboration between material scientists and gear manufacturers, the potential for innovation in material selection and design will continue to shape the future of gear technology, ushering in an era of advanced power transmission solutions.